Introduction
Hardfacing is a process used to apply wear-resistant materials to the surface of metal components, extending their lifespan and enhancing performance in demanding conditions. This technique involves the deposition of harder materials onto softer substrates to protect them from abrasion, erosion, corrosion, and other forms of wear. Among the materials used for hardfacing, carbide ceramics stand out due to their exceptional hardness and durability. This article explores specific carbide ceramics, their properties, applications, and benefits in detail.
1. Silicon Carbide (SiC)
Properties
SiC ceramic is renowned for its outstanding properties, making it a superior choice for hardfacing applications. Key properties include:
- High Hardness: SiC has a hardness of 9.5 on the Mohs scale, making it one of the hardest materials available, second only to diamond and boron carbide.
- Thermal Conductivity: SiC exhibits high thermal conductivity, which allows it to efficiently dissipate heat and maintain structural integrity under high-temperature conditions.
- Thermal Shock Resistance: The material can withstand rapid temperature changes without cracking due to its excellent thermal shock resistance.
- Chemical Resistance: SiC is highly resistant to chemical corrosion, maintaining its properties in both acidic and basic environments.
- Low Thermal Expansion: The low thermal expansion coefficient of SiC contributes to its dimensional stability under varying thermal conditions.
- High Strength: SiC maintains high strength even at elevated temperatures, making it suitable for high-stress applications.
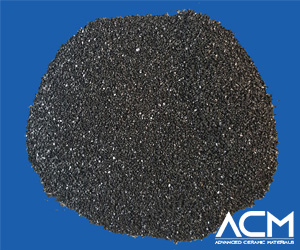
Applications
SiC's durability under fluctuating temperatures and its resistance to wear make it indispensable in industries requiring high performance under harsh conditions. Its use in semiconductors also highlights its importance in advancing technology. Here are how silicon carbide ceramic used in hardfacing applications:
- Semiconductor Manufacturing: SiC is used in the production of semiconductors due to its ability to maintain performance at high temperatures.
- Abrasive Materials: The hardness of SiC makes it ideal for use in abrasives and cutting tools.
- Refractory Materials: Its thermal stability makes it suitable for kiln furniture and other high-temperature applications.
Silicon carbide's utility extends to the field of high-voltage and high-frequency electronics. Its electrical properties allow devices to operate at higher efficiencies compared to traditional silicon. Moreover, the use of SiC in armor plating showcases its versatility, providing lightweight yet highly durable protection.
2. Boron Carbide (B4C)
Properties
Boron carbide is one of the hardest known materials, surpassed only by diamond and cubic boron nitride. Key properties include:
- High Hardness: The Mohs hardness of boron carbide is between 9 and 10, earning it the nickname "black diamond."
- Low Density: It has a low density of about 2.52 g/cm³, making it a lighter choice for armor making.
- Chemical Inertness: B4C is highly resistant to chemical reactions, maintaining stability in various environments.
- Nuclear Absorption: B4C has a high cross-section for capturing neutrons, making it valuable in nuclear reactors.
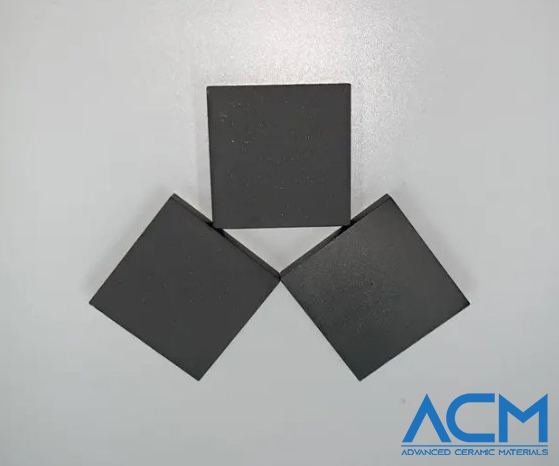
Applications
The combination of lightweight and high-impact resistance makes B4C particularly valuable in defense applications. Its use in nuclear reactors also underscores its importance in energy sectors.
- Ballistic Armor: Due to its hardness and low weight, B4C is used in personal and body armor.
- Abrasive Materials: Its extreme hardness makes it ideal for use in abrasives and cutting tools.
- Nuclear Applications: B4C's ability to absorb neutrons makes it useful in controlling nuclear reactions.
Boron carbide's role in defense is significant, as it allows for the creation of lightweight body armor that provides high levels of protection without compromising mobility. In industrial settings, B4C abrasives are used in lapping and polishing applications, ensuring precision and efficiency.
3. Titanium Carbide (TiC)
Properties
Titanium carbide (TiC) is a ceramic material known for its outstanding properties, making it highly suitable for hardfacing applications. Key properties include:
- High Hardness: TiC has a hardness of 9-9.5 on the Mohs scale, making it one of the hardest ceramic materials.
- High Melting Point: TiC has an exceptionally high melting point of approximately 3,160°C, allowing it to maintain its structure and properties at very high temperatures.
- Good Thermal Conductivity: TiC exhibits good thermal conductivity, which helps in dissipating heat and maintaining its structural integrity under thermal stress.
- Thermal Shock Resistance: TiC can withstand rapid temperature changes without cracking, similar to other carbide ceramics.
- Chemical Stability: TiC is chemically stable and resistant to oxidation, ensuring durability in various environments.
- Low Density: Despite its hardness and high melting point, TiC has a relatively low density compared to other refractory materials, making it suitable for applications where weight is a concern.
Applications
TiC's hardness and thermal stability make it ideal for high-hardness applications and environments requiring materials that can maintain their integrity under stress. Its use in aerospace highlights its importance in advanced engineering applications.
- Cutting Tools: TiC is used in tool bits for machining and cutting applications due to its hardness.
- Wear-Resistant Coatings: Applied to surfaces that endure significant wear, extending their service life.
- Aerospace Components: Its thermal and mechanical properties make it suitable for high-performance aerospace applications.
Titanium carbide's application in aerospace components includes jet engine parts and turbine blades, where materials are subjected to extreme conditions. The use of TiC in these areas ensures longevity and reliability, critical for safety and performance.
Conclusion
As technology advances, the development of new carbide ceramics and the enhancement of existing ones will likely continue. Research into improving the synthesis and application processes of these materials could lead to even more robust and efficient solutions for industrial challenges. The ongoing exploration of nanotechnology and its integration with carbide ceramics holds promise for the next generation of high-performance materials. Advanced ceramic materials will play a significant role in these developments, offering even greater possibilities for innovation and performance in hardfacing applications. Advanced Ceramic Materials (ACM), a leading supplier of carbide ceramics and other ceramic materials, continues to support these advancements by providing high-quality materials for various industrial applications.
REVIEWS
{{viewsNumber}}
Thought On "{{blogTitle}}"
LEVE A REPLY(Cancle reply)
Your email address will not be published. Required fields are marked*
{{item.children[0].name}}
{{item.children[0].created_at}}
{{item.children[0].content}}
More Replies
LEAVE A REPLY
Your email address will not be published. Required fields are marked*